As the industry matures, maximising the value that can be captured from known reserves is more important than ever. However, in declining fields, both operational and cost effectiveness need to be exemplary if production levels are to return a viable profit.
There is much to be said for marginal gains – the practice of making the tiniest of tweaks that, when added together, deliver a significant improvement on standard ways of working. But approaching a project from a completely new angle can also deliver the required results. This was demonstrated in a project in the Texas Panhandle where new technologies and new ways of working delivered increased production rates at reduced cost when compared to traditional methods.
Project background
The project was a two well re-entry campaign in the Texas Panhandle. It was part of a wider campaign to intercept fractures and access untapped reserves to boost production and revitalise a field that had not been producing for many years.
The two wells were primarily gas producers, with condensate and water also being produced. Both wells were to be drilled underbalanced to reduce formation damage and to avoid significant impact on subsequent production.
Underbalanced Coiled Tubing Drilling (UBCTD) was seen as the best way to drill the reservoir because it provides continuous stable underbalanced bottom hole pressure, as well as fast, safe and effective operation with two phase drilling fluids.
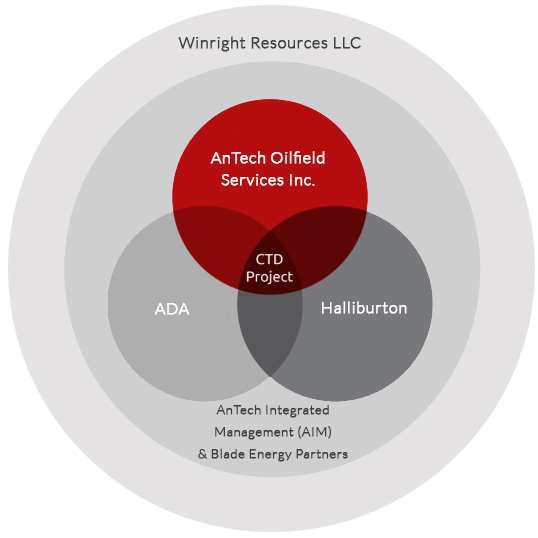
New technologies
In the early stages of the project, it was decided that wellsite data acquisition, offsite support for data analysis and information from downhole sensors would be aggregated and shared with all parties in real time.
Doing this would mean all parties would always have a complete, real time picture of what was happening on the wellsite, enabling rapid decision-making.
Having the data in real-time would also allow the use of RockSense, AnTech’s proprietary synthetic porosity algorithm, which distinguishes between different formations by combining downhole and surface data in real time to give an at-bit measurement of porosity.
It offers two considerable advantages over traditional geosteering techniques. First, wired telemetry has a high data rate, so multiple measurements can be made for every foot drilled and operators can gain inch-level resolution. Second, because the data delivered is representative of conditions at the bit – not 20-25ft behind it – the driller can deliver an optimally placed wellbore, with more feet drilled in the target zone.
New ways of working
To allow real time data aggregation, a much more collaborative approach than is typical, was needed.
Usually, the four principal parties in a UBCTD campaign (the directional downhole tools provider, the coiled tubing service company, the underbalanced drilling fluids package and the operator) each uses their own data acquisition system. In this scenario, an incomplete picture is available to any party at any given time and there are delays in decision making while data from the other parties is requested, collated and analysed.
In this project, AnTech, the directional service provider, took on the role of aggregating the data. In advance of arriving at the wellsite, they provided the conversion kit to convert the rig to e-line (slip ring collector, collector bulkhead) and enable the CT unit to run e-coil. AnTech also provided pre-job engineering, pre-job project management, and the downhole equipment. Halliburton provided the CT unit and pumps, ADA provided the fluids separation package and Blade Energy Partners provided pre-job engineering and wellsite supervision/project management on-site. (See Figure 1.)
To view the full article, please visit: Oilfield Technology or contact us