Underbalanced Coiled Tubing Drilling (UBCTD) offers operators a way to capture significant extra value out of known reserves. In fact, it has been comprehensively shown that, when applied correctly, the technology can deliver increased production rates at reduced cost when compared to traditional methods. It therefore makes maximising returns from declining fields a viable and attractive value proposition.
However, in a traditional site set up, the technology is still held back by traditional ways of working. There are typically four principal service companies involved in a UBCTD campaign: the directional downhole tools provider, the coiled tubing service company, the underbalanced drilling fluids package and the operator. Each company uses its own data acquisition system (DAS). Typically, this means an incomplete data picture is available to any party at any given time. Consequently, there are delays in decision making on-site while data from the other parties are requested, collated and analysed.
New proprietary technologies have come along that remove the delays inherent in these traditional ways of working. They enable real time decision making and take the productivity, operational and cost effectiveness of UBCTD together to the next level. As such, it opens up new opportunities for operators with declining fields.
An example of such technology is RockSense that was demonstrated in a project led by AnTech in the Texas Panhandle. RockSense is AnTech’s proprietary synthetic porosity algorithm. RockSense has the ability to distinguish between difference formations by combining downhole and surface data in real time to give an at-bit qualitative measurement of porosity. It offers two considerable advantages over traditional geosteering techniques. Because wired telemetry has a high data rate, multiple measurements can be made for every foot drilled and operators can gain inch-level resolution. And because the data delivered are representative of conditions at the bit – not 20-25ft behind it – the driller can deliver an optimally placed wellbore, with more feet drilled in the target zone.
To enable the use of technologies such as RockSense, a complete real time data picture is required. This means all parties involved in a project have to share their data in real time. For this to be achieved – and for operators to be able to take advantage of the enhanced capabilities technologies such as RockSense deliver – a different way of working that involves a very much more collaborative approach from the very earliest stages of a project needs to be embraced by the operator and the service companies.
It’s a way of working that was embraced by an operator in the Texas Panhandle. Specialist contractors were utilised for each major component of the project and tightly integrated from the earliest stages using project management best practices. Its success showed the value of collaborative working in combination with UBCTD and digital technologies.
Project background
The project was a two well re-entry campaign in the Texas Panhandle. The wells were part of a wider campaign to revitalise a field that had been producing for many years. The overarching aim of the wider campaign was to intercept fractures and access untapped reserves to boost production.
Underbalanced drilling was considered the best way to increase production because .it is known that preventing a formation from becoming overbalanced at any time can have a significant impact on production. Indeed, the expectation was that the production would remain high for a prolonged time due to the benefits of drilling underbalanced.
UBCTD was chosen specifically because of the particular nature of the two wells. They were primarily gas producers, with condensate and water also being produced. UBCTD was seen as the best way to drill the reservoir underbalanced because it provided continuous stable underbalanced bottom hole pressure, as well as fast, safe and effective operation in two phase flow.
In the early stages of the project, the operator decided to use new digital technologies for wellsite data acquisition, offsite support for data analysis and downhole sensors, by aggregating the data from all parties involved. By doing this, all parties would have a complete picture of what was happening on the wellsite and real time decision making would be improved.
In order to enable this way of working, a great deal of time and effort was given to the planning phase prior to work starting on site – considerably more than would be traditionally expected. However, the operator recognised that such detailed planning and preparation was critical to the success of the project and encouraged the approach, creating a fully ingtegrated and effective working culture and operation.
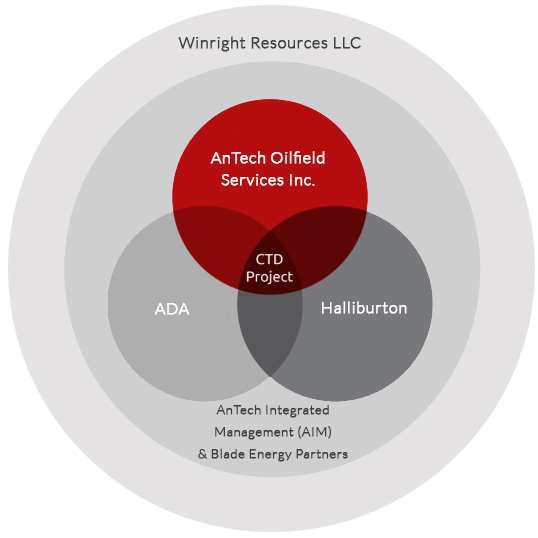
The role of aggregating the data was taken on by AnTech, the directional service provider. AnTech also provided pre-job engineering, pre-job project management, downhole equipment and data aggregation. Halliburton provided CT unit and pumps. ADA provided the flow back package. Blade Energy Partners provided pre-job engineering and wellsite supervision/ project management on site. (See Figure 1.) To enable the CT unit to run e-coil, AnTech provided the conversion kit to convert the rig to e-line (slip ring collector, collector bulkhead), work that was done well in advance of arriving at the wellsite.
This collaborative way of working proved beneficial very early on in the project lifecycle.
Early planning and collaboration helps address challenges
The principal challenge needing to be addressed early on in the project was cost. The critical requirement was to stay in AFE, with a related aim of showing that UBCTD could be carried out cost effectively in the US and generate a significant ROI.
Wellbore stability in the build section and water were two areas considered to be of particular concern.In terms of wellbore stability in the build section, the candidate wells had to be evaluated for stability in the overburden immediately above the pay zone. In terms of water, assessment was required because wells in the area had a history of watering out, so there was a risk of hitting water, which would significantly harm ROI.
The large amount of time and effort put into the planning work was critical in ensuring that the wells were drilled as planned, that there were no surprises and challenges could be mitigated. To assess these challenges, a Hazard Identification study (HAZID) and Drill Well On Paper (DWOP) exercise were carried out before starting work with all the major service companies attending in person during the planning phase. This work helped to identify the major risks and mitigations required to complete the project successfully.
The planning showed that only one candidate was able to be drilled underbalanced with an acceptable level of risk. All other wells had substantial amounts of shale interbedded with the limestone in the build section. There was therefore a high risk of shale instability. It was for this reason that the second well had an intermediate section drilled and cased by a conventional drilling rig.
The planning also resulted in several other important outputs. It enabled the creation of a detailed set of written procedures that outlined exactly how the project was to be carried out. It also enabled contingency planning to deal with wellbore stability in the build section and water in the horizontal to be carried out. These contingencies included an expandable liner being kept on standby as a contingency for the wellbore stability and inflatable plugs being available in case of hitting water. The planning demonstrated that such contingencies were a sensible investment.
To view the full article, please visit: MED OIL & GAS or contact us