Fatigue life modeling has extended the economic life of Coiled Tubing (CT), making the ability to predict the safe working life of CT string is an essential part of coiled tubing operations. New applications like drilling and fracturing can now be undertaken with confidence and success, revolutionizing the CT industry.
A coiled tubing string becomes unsuitable for continued use if the accumulated fatigue exceeds the limits set by the operating company. There are several methods utilized to predict the service life of the coiled tubing string. Some are quite simple; some can be more complex. The simplest approach that is easy to implement would be a “running-feet method”. A total footage for the CT string run into wells is recorded, when a specified limit is reached, a decision to retire the string is made. Typical length would depend on the CT string properties, and can vary from 250,000 ft up to 750,000 ft. With new coiled tubing developments, this range limit can now be increased. However, the range limit is based on the previous experience with similar tubing performing similar operations under similar well conditions. A company cannot simply extend the same limits to a different size string or different well operating conditions as the fatigue life will be different.
An upgrade to the running-feet method would be to account for variations in the stresses along the string. Typically, certain sections of coiled tubing string are subjected to more frequent bending over the reel and gooseneck, therefore, reducing the fatigue life of those sections faster comparing to the rest of the string. Recording accumulated fatigue in each section, typically 500 ft long, will help to get more accurate results of the string condition. Currently, when a certain section or sections of the tubing reach a fatigue life limit that was previously set by the company, the tubing is cut from the bottom, so a highly fatigued section would be positioned deeper downhole during subsequent operations. In turn, a section with higher fatigue life would be on the reel and gooseneck and operate until it reaches its limit as well. The CT engineer must be aware of the well depth that the string is going to be used in, to make sure that the section with the least fatigue life is not subjected to high bending stresses during operation. The length of the tubing removed should be at least the distance between the reel and the guide arch. If necessary, additional pipe section might be cut-off to adjust for string placement in the well.
If the CT string still has enough fatigue life left, but has reached a certain length, where it is no longer suitable to operate in the given well depths in the region it operates, it is time to retire it or it can be re-sold to a region where existing wells are shallow enough for that length of tubing. Loss of the integrity of any tubing string in any condition makes it unfit for the service.
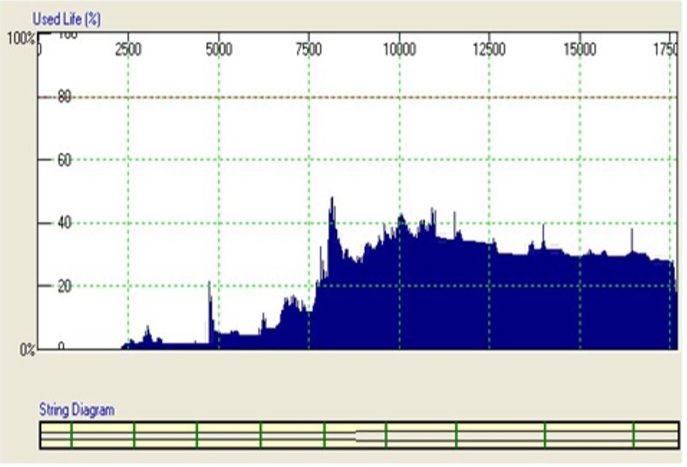
Fig. 1 - CT String Accumulated Fatigue
Lastly, the most accurate model to predict fatigue life of the string is theoretical modeling. It involves using various algorithms to predict and estimate the fatigue damage due to proposed CT operation. String Management software allows tracking the fatigue status of a CT string in order to avoid costly failures at the wellsite while maximizing the usage of the pipe before it is retired from Service (Fig. 1). The essence of fatigue tracking is to know exactly which section of pipe is being bent at any given moment, and what the prevailing conditions are at the time.
Author: Marat Seitimov