Learning on the job is a great way of gaining experience but I think we would all be surprised if an airline pilot hadn’t spent some time on a simulator before flying passengers. The reason is that the cost of failure, crashing, is expensive in both human and financial terms. It is much better to simulate events offline. Oilfield operations, where high pressures, hazardous chemicals and complex systems are involved are no different. Digitally simulating oilfield operations ahead of time saves cost, prevents accidents, and speeds operations. That is why feasibility studies are so important.
The key to getting the most out of technology is understanding when not to use it. After all, the most advanced and cutting edge technology in the world is useless to us if it is not used within the correct application.
This is especially the case for broad use technologies like Coiled Tubing Drilling (CTD) that can be employed in a range of applications, but are complex in their specifics. For example, CTD can be a low cost solution in some applications, while in other applications it requires larger investment in order to achieve a larger reward. In remote operations CTD has the advantages of low mobilization cost and a small crew requirement, which maximizes ROI by delivering the same production as a conventional rig at a lower overall project cost. However, when drilling a depleted reservoir underbalanced with two-phase fluid system of water and nitrogen, the spread rate can be higher than a conventional rig operation but the return on investment is realized through achieving production levels that could not be achieved using a conventional rig drilling overbalanced.
A sales representative selling a broadly applicable technology such as CTD can seem disingenuous by listing all the potential benefits of the technology, because while these benefits are achievable in the broadest sense, the end client may not actually realize all of the benefits in every application. It is a case of identifying that the right technology is being used in the right configuration in order to maximize value to the end client. Therefore, any high quality feasibility study must take into account both technical and commercial feasibility.
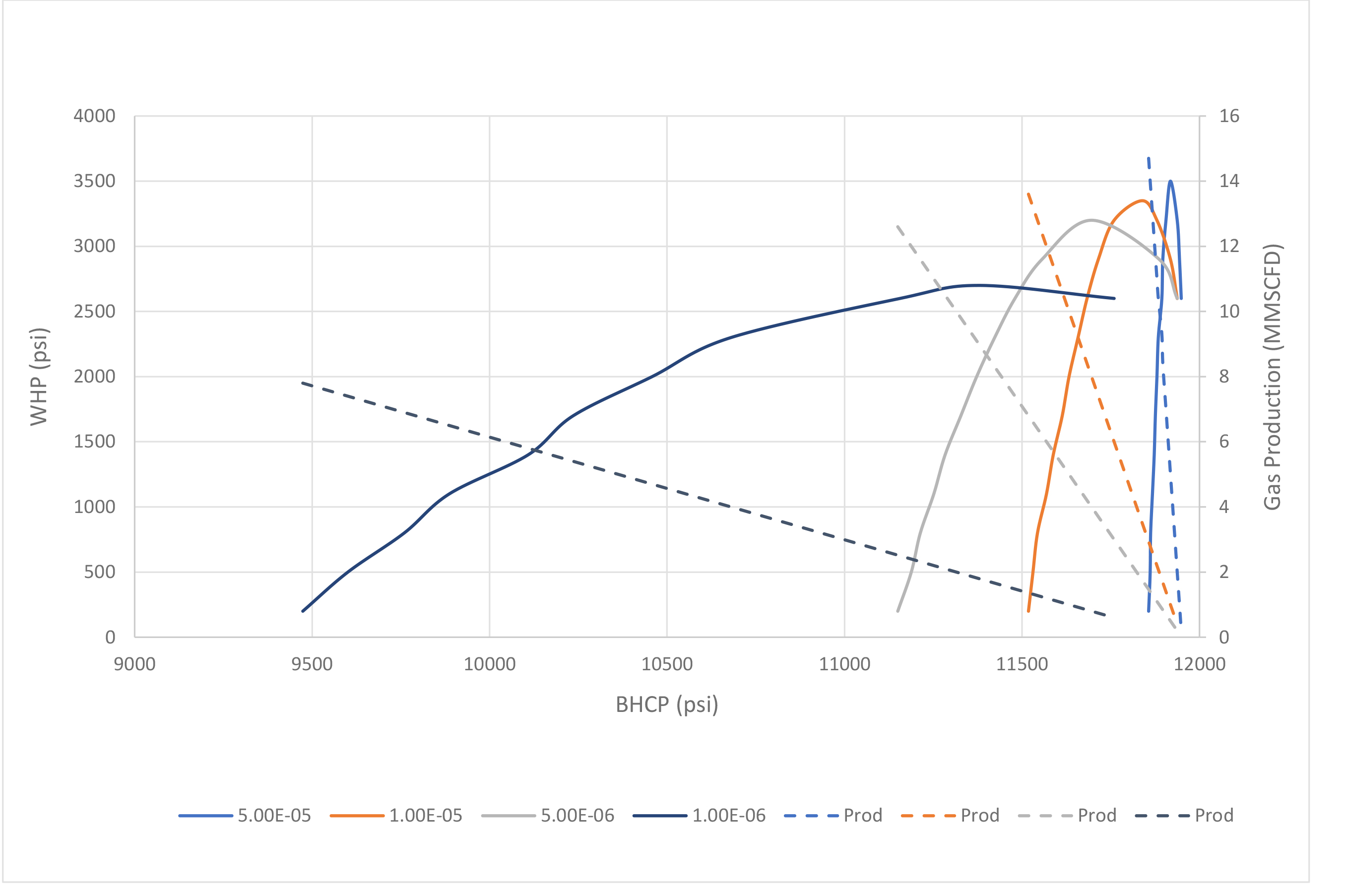
To illustrate this point for the sake of this article, we will focus on the fundamental steps and points of consideration that would be undertaken during a feasibility study for gas wells being re-entered and drilled, the assumption being that the well should be drilled underbalanced with coiled tubing in order to avoid formation damage, as well as to maximise productivity from the well.
A feasibility study can be thought of as a “negative proof”. In maths, a negative proof is a demonstration that a particular problem cannot be solved as described in the claim. In this case, the claim is that drilling the well using CTD is the technique most likely to maximise success and return on investment. In actual fact, a “feasibility study” is quite the opposite of how it sounds, because while something can be feasible, it may not always be desirable given the specific circumstances, and to ignore that fact would be a disservice to the end client.
On this basis, the first step is to discuss with the client their rationale for wanting to apply the technology to their field in the first place. The operator understands their fields and their operational challenges better than anyone and they will have been attracted to the technology based on solving specific problems. A quick phone call can often be enough to gauge whether or not there is a suitable application for CTD or not. At this point it is also important to answer a few basic operational questions, such as identifying any access restrictions, determining the size of the pad, and describing the general drilling experience in the target formations.
Assuming the project still looks attractive after that first discussion, the next step is to identify the level of detail required from the study, which will determine how deep into the technical analysis to go. Some operators may want an answer as fast as possible whereas others may require more detailed analysis, even if the result is that the specific project or well is indeed not feasible. This may be due to the fact that they wish to build institutional knowledge around the technology and understand how to evaluate their other assets in-house in order to make best use of the benefits of the technology.
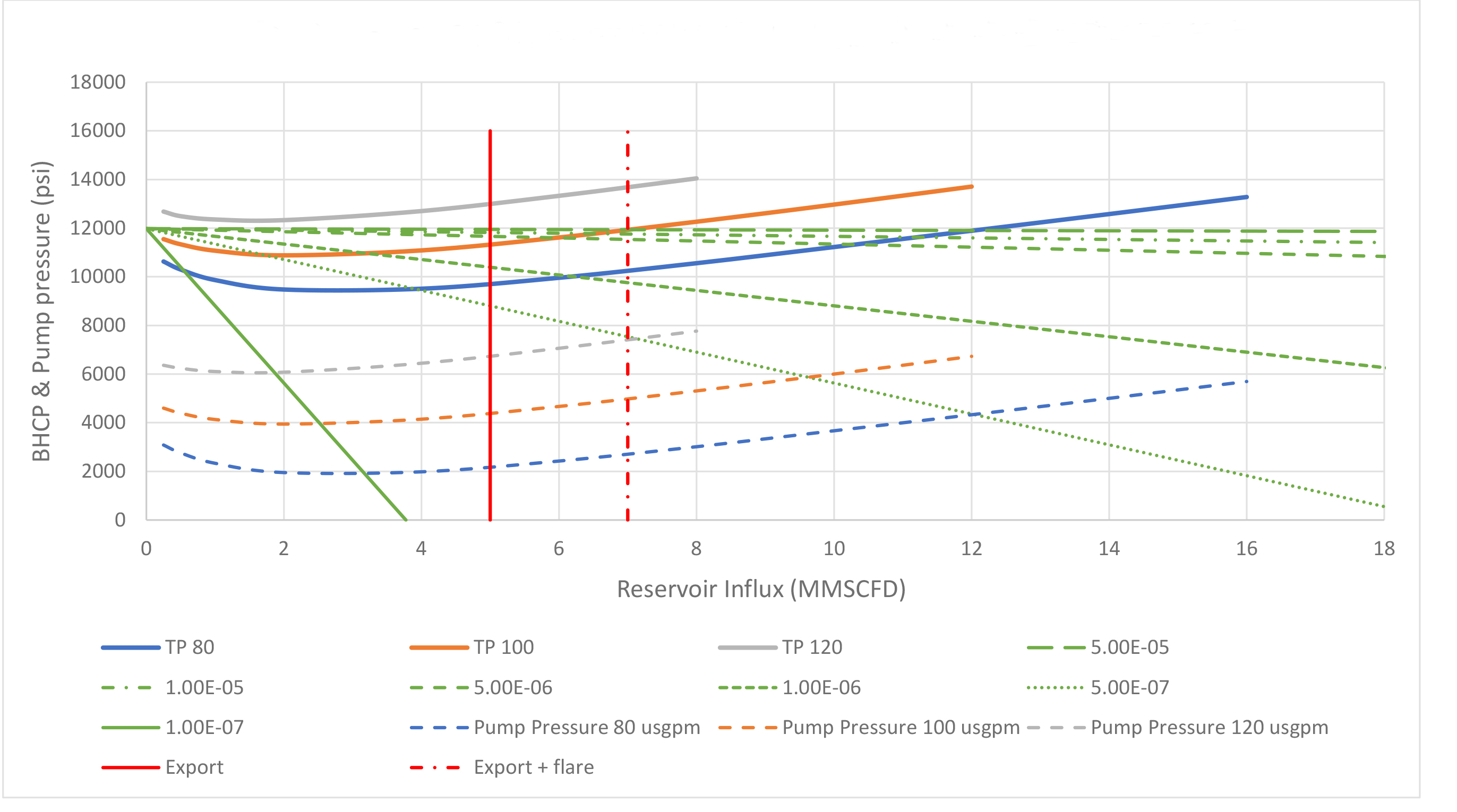
The core advantage of coiled tubing when drilling is pressure control. Continuous pipe and equipment rated for 15,000 psi wellhead pressure as standard gives a lot more flexibility in terms of drilling both underbalanced and at balance with formation pressure. When drilling underbalanced or at balance on a conventional rig, the rotating control device (RCD) has a much lower pressure rating than the rest of the pressure control equipment. A standard RCD has a pressure rating of 2,000psi static, 1,200psi when stripping and even less when drilling ahead. However, on a coiled tubing unit the rotating control device is replaced by a stripper that is capable of operating up to the same pressure as the blow out preventers in most instances. UBCTD has the safest possible set up from a well control stand point. Also, this means that there is much more scope to adjust the well parameters on the fly based on live observations while drilling the hole section. For example, when drilling through a highly productive fracture.
The drilling choke is another key piece of equipment on a UBCTD project. Flow from the well is controlled through the circulating fluid and the back pressure provided by a choke. Chokes can be remote controlled and manual or automatic.
There are four major components to a UBCTD feasibility study: wellbore hydraulics modelling, coiled tubing modelling, equipment specification and cost estimation.
Prior to working on any hydraulics modelling, a draft trajectory should be made. The trajectory will produce the first set of questions to be answered, which will constrain the well design. For example, can the well be sidetracked and landed within the target formation, or are multiple formations drilled through? Any formation drilled through must be assessed for wellbore stability, and it must be determined whether or not the formations can be safely in communication with each other. At this stage it will also be possible to start making an assessment of total project length, and therefore budget, which can be refined as the hydraulics modelling progresses.
Once the trajectory has been designed, the hydraulics models are built in a steady-state multi-phase flow modelling software and a critical factor analysis is carried out. This will give an idea of the fluid type and weight that will be used. At this stage it is important to determine if a single phase fluid such as water or brine will be used, or a two-phase fluid such as co-mingled water and nitrogen. Once the critical factor analysis modelling has progressed to such a point where some certainty is known about the operational limits of the fluid type and weight and the well productivity, then a tubing forces analysis can be carried out in order to understand the coil size required to achieve the target lateral length. The design of the coiled tubing effects the hydraulic response of the well and vice versa. For example, a larger outer diameter of the coiled tubing will reduce the annular space and therefore increase the bottom hole pressure and the annular velocities, both of which are critical factors to consider in the well design. However, from the other analytical perspective, the injected fluid and the produced gas volumes will effect buoyancy, annular pressures, and pump pressures, which will in turn effect the buckling limits, available weight-on-bit, lateral reach, overpull and coil life.
Once a coiled tubing size has been selected, the models are run in order to determine the relationships between injected fluids, reservoir productivity, circulating rate and wellhead pressure. The primary concern is to address how the well can be kept safely under control during the entire operation. In underbalanced operations, the primary well control is provided by a combination of flow and pressure control equipment and secondary well control is provided by the BOPs. Therefore, understanding the potential gas production is important for understanding controllability, fluid and equipment requirements in order to drill the well safely. In the feasibility study stage it is particularly important to focus on the extremes. Figure 1 shows analysis at a range of productivity indices, Figure 2 shows tubing performance and productivity for one particular operating condition, and Figure 3 shows how well production varies with pump rate and wellhead pressure.
Coiled tubing has a distinct advantage in that once stable circulating parameters are obtained then they may be able to be held steady for the entire hole section. This is very important in gas systems where transient effects are difficult to control but also it prevents overbalanced situations inadvertently occurring and minimizes the chance of hole collapse through varying wellbore pressures.
One question that may not be intuitive to those not familiar with underbalanced drilling is that, as with the coiled tubing string design and trajectory, there is a limitation on achievable lateral length due to the wellbore hydraulics. It is possible to be underbalanced at the heel of the well and overbalanced at the toe. This is an important factor to take into account as it is possible to take losses or overpulls at the toe due to poor hole cleaning when the well is producing as expected from the heel. This can be controlled to a certain extent through operational procedures, e.g. flow rates and optimized fluid weights, and well design e.g. hole size and casing size.
It is clear by now that the nature of UBCTD feasibility studies is for an iteration of the models and design considerations. However, slowly but surely the critical factors are narrowed down. Once the hydraulics models are at this stage then the coiled tubing models can be revisited for optimization. With the combination of the hydraulic and coiled tubing models the final achievable lateral reach and well productivity can be calculated. An expected coiled tubing grade and draft design should also be specified at this stage as it is important both from an engineering stand point but also cost and durability stand point.
One thing that has not been mentioned so far but is critical throughout the analysis consideration must be given to what would happen during real life operations. A model will provide a solution but experience must determine if that solution is achievable using the equipment and personnel available. “What if” scenarios need to be addressed in the feasibility study, although not in great depth. It is important that the ability to deal with the unexpected is taken into account from the beginning, especially in terms of safe operations.
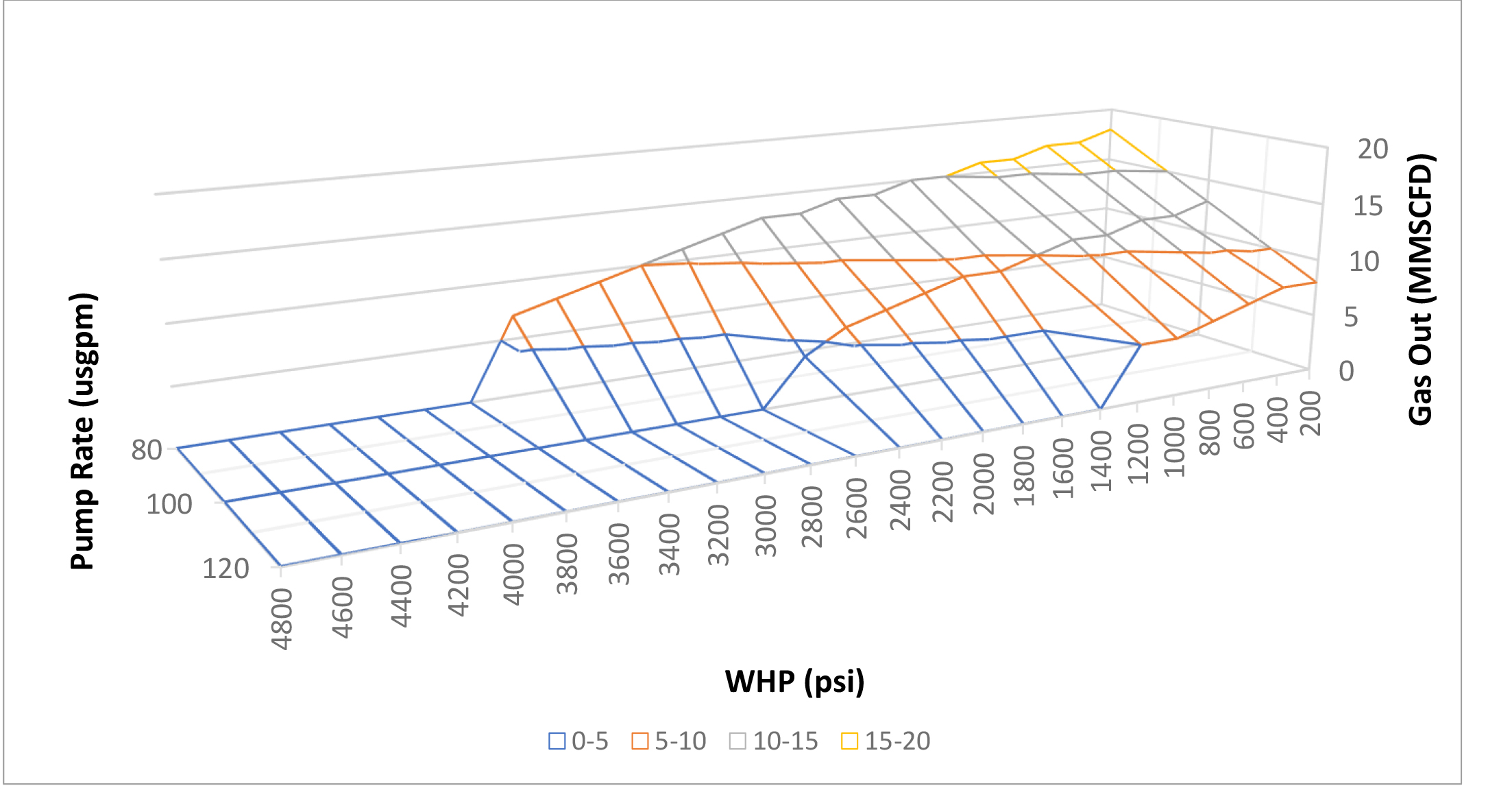
In terms of the equipment required for a UBCTD campaign, the major components are the coiled tubing equipment including pumps, the returns system (e.g. fluids, solids, and gas handling) and the directional package. When drilling with a two phase system, e.g. water and nitrogen, there will be additional pumps, storage tanks and logistics. If the intention is to push any produced gas to the sales line then consideration must be paid to the maximum nitrogen content allowed and maximum line pressure.
To view the full article, please visit: Oilfield Technology or contact us